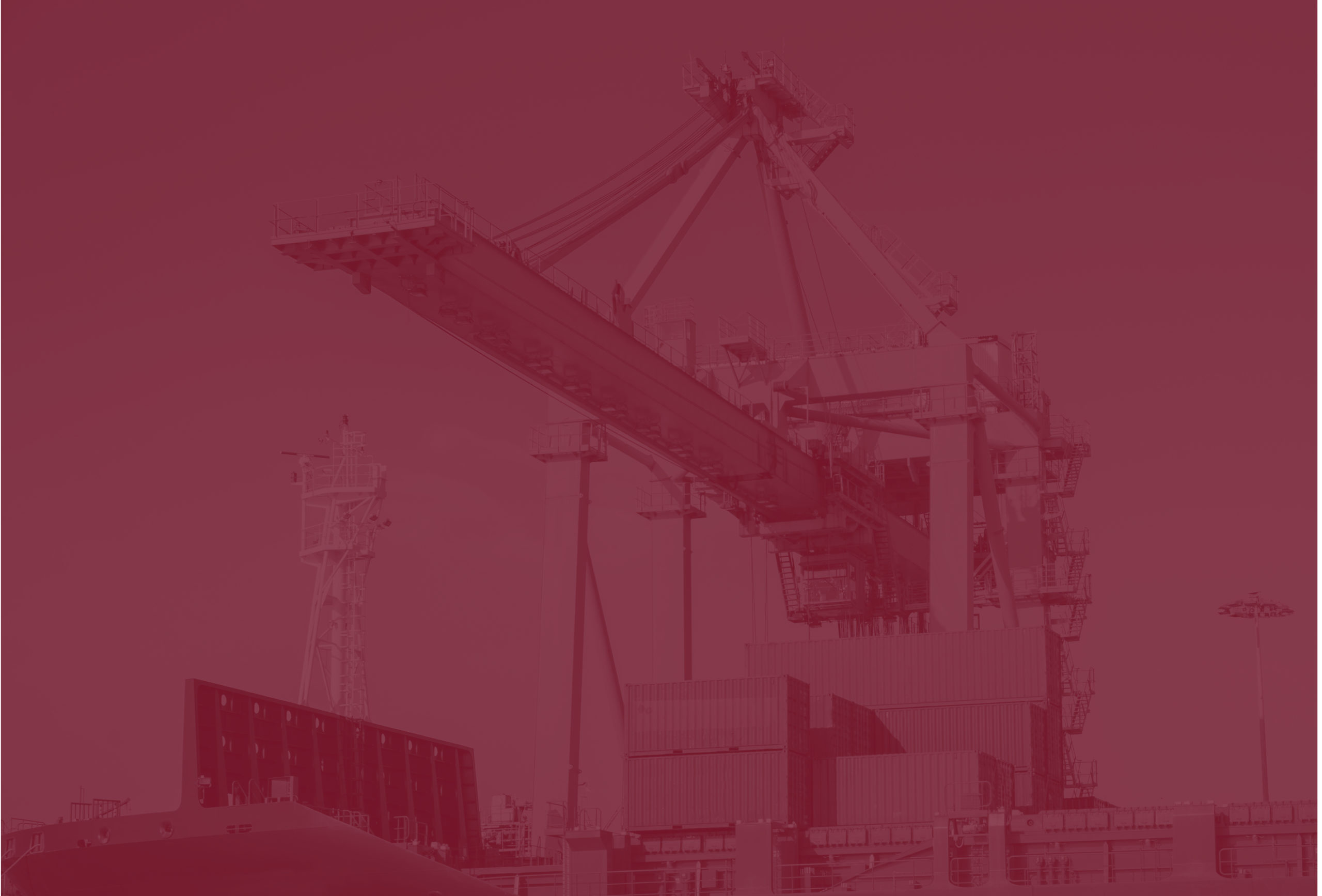
port equipment maintenance
Learn, how you can optimize port equipment maintenance to increase operational efficiency, avoid downtime and prolong equipment lifetime.
Better lubrication means better economy
As in all other industries relying on heavy machinery, proper lubrication plays a major role in securing productivity. Well-lubricated port cranes are reliable and safe, and demand a minimum of downtime and repair costs.
Port operators should focus on four key elements, that are essential to maintaining the performance and longevity of port equipment and should be an integral part of any crane maintenance program:
Get the right lubricant
The selection of the right lubricant is critical to ensuring effective lubrication of the crane components. The lubricant must be compatible with the materials and components being lubricated, provide appropriate levels of protection against wear and corrosion, and operate effectively under the expected operating conditions.
Find the right frequency
The frequency of lubrication depends on factors such as the type of lubricant used, the operating conditions, and the manufacturer’s recommendations. Regular lubrication is critical to prevent wear and corrosion.
Do it right
There are several methods for applying lubricant, including manual lubrication, automatic lubrication systems, and centralized lubrication systems. The method used depends on factors such as the size of the crane, the location of the lubrication points, and the frequency of lubrication.
Inspection and maintenance
Regular inspection and maintenance of the crane’s lubrication system are critical to ensure that the lubrication system is functioning properly and that all lubrication points are receiving adequate lubrication. This includes checking for leaks, blockages, and other issues that could affect the performance of the lubrication system.
Learn more
Want to learn more and discover efficient solutions for port equipment maintenance?
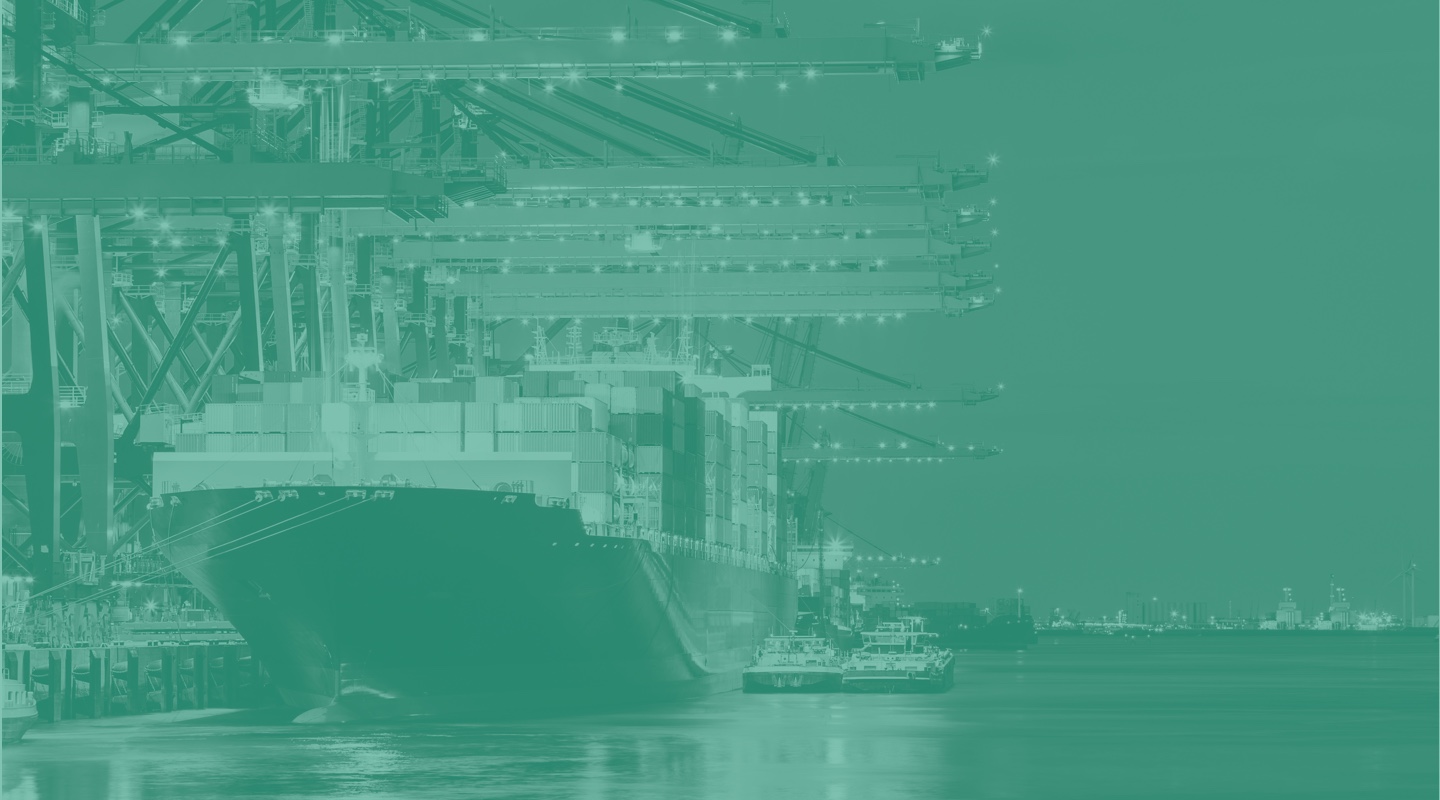
Ports never sleep, but nor does rust. That makes fast and precise lubrication critical, and that’s exactly what our port lubrication solutions offer.
Thomas Cramer
CCO, HOVE
Predictive maintenance: Identify issues before they occur
Predictive maintenance is a proactive approach that uses data analysis and monitoring to predict when equipment failure is likely to occur. It’s a valuable tool for port operators looking to optimize their equipment maintenance programs, reduce downtime, and improve port equipment efficiency and reliability.
By using advanced monitoring technologies, port operators can gather real-time data on the performance of their equipment, and use this data to identify potential issues before they occur. By leveraging the power of data analysis and monitoring, port operators can stay ahead of potential equipment problems and keep their operations running smoothly.
Optimize performance across your port facilities
Using predictive maintenance, port operators can predict when equipment failure is likely to occur and schedule maintenance activities in advance. This can help to reduce downtime and repair costs by allowing maintenance to be scheduled during planned downtime periods, rather than during unscheduled downtime events caused by unexpected equipment failures.
In addition, predictive maintenance can help to optimize equipment performance and extend equipment life by identifying potential issues before they become serious problems. By addressing issues early, port operators can avoid more costly repairs or equipment replacement, and ensure that their equipment is operating at peak efficiency.
Want to try predictive maintenance?
Hove Smart Lube is a field-proven digital solution for any type and size of port. Plug it into your operations, get full traceability and maintain control of everything linked to lubrication.
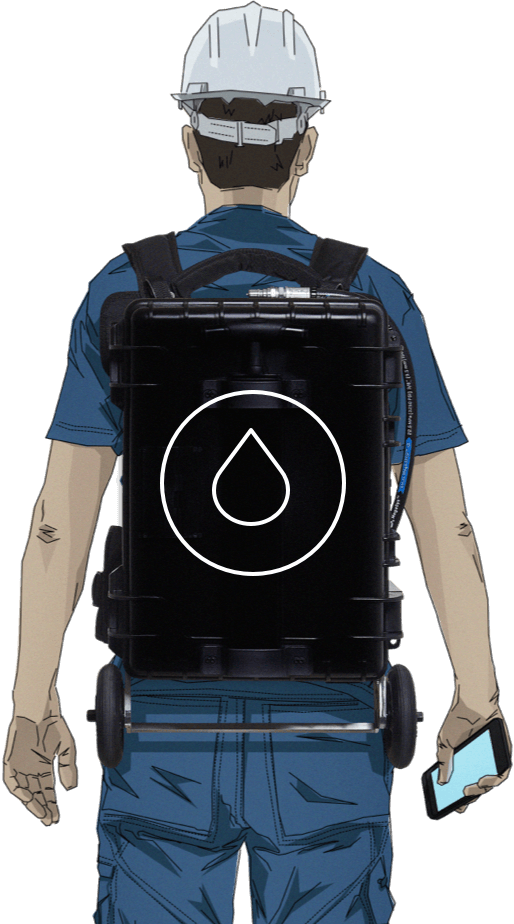
Maintain port cranes smarter
Hove Carry is a portable lubrication solution for ports. Its compact design, battery-powered pump, and digital interface give you full mobility and easy tracking and documentation.
Sign up for the Hove newsletter
Get insights and news on wind turbine maintenance. For wind farm owners, operators, servicing companies, and wind turbine technicians.
port equipment maintenance FAQ
1. Monitoring to detect any potential problems or issues that may affect their performance.
2. Preventive maintenance to prevent equipment failures and extend the lifespan of the equipment.
3. Corrective maintenance: repairing or replacing damaged or faulty parts to restore the equipment to its normal operating condition.
4. Predictive maintenance that allows maintenance to be scheduled in advance, reducing the risk of downtime and repair costs.
5. Training and education to ensure that personnel are knowledgeable about equipment operation, maintenance requirements, and safety procedures.
6. Documentation and record keeping for tracking maintenance schedules, identifying trends, and ensuring compliance with regulations and standards.
Preventive maintenance involves scheduled maintenance activities designed to prevent equipment failures and extend the lifespan of the equipment. This includes activities such as oil changes, filter replacements, lubrication, and cleaning.
Documentation and record keeping: Accurate and detailed documentation of equipment maintenance activities and records of equipment service history are important for tracking maintenance schedules, identifying trends, and ensuring compliance with regulations and standards.
Get in Touch
If you have any questions about Hove products, quotes and services or would like to hear more about how Hove can benefit your business, please don’t hesitate to contact us. We are here to help.